If you have a GE top load washer and you’re finding that your clothes are still soaking wet after the spin cycle, you could be dealing with a number of different issues. The good news is that many of these problems are fairly easy to diagnose and fix yourself, without having to call in a repair technician.
In this article, we will explore nine possible reasons why your GE top load washer might not be spinning clothes dry.
First and foremost, one common cause of this issue is an unbalanced load. If your washer is overloaded, or if the clothes inside are distributed unevenly, it can cause the washer drum to spin unevenly as well, leading to poor water drainage and damp clothes.
Another possible culprit is a faulty lid switch. This switch is what tells the washer to start and stop spinning, so if it’s not working properly, your washer may fail to spin completely.
Other potential causes of a GE top load washer that’s not spinning clothes dry include issues with the drive belt, the drive motor, the transmission, or the clutch. There could also be a problem with the washer’s drainage system, either due to clogs or a malfunctioning pump.
By identifying the specific cause of your washer’s spinning problems, you can take steps to fix the issue and get your clothes as dry as possible. Keep reading to learn more.
GE Top Load Washer Not Spinning Clothes Dry – Causes & Fixes
Let’s see the solution.
Reason | Causes | Fixes |
---|---|---|
Overloaded washer | Overpacking the washer drum | Follow load capacity guidelines |
Faulty lid switch | Lid switch not engaging | Check for physical damage or disconnection |
Unbalanced load | Uneven distribution of clothes | Avoid overloading the washer |
Broken drive belt | Worn or frayed drive belt | Replace the drive belt |
Clogged drain pump | Debris or blockage in the drain pump | Clean or replace the drain pump |
Faulty motor coupling | Worn or broken motor coupling | Replace the motor coupling |
Worn out clutch assembly | Worn or damaged clutch assembly | Replace the clutch assembly |
Defective transmission | Faulty or damaged transmission | Replace the transmission |
Malfunctioning timer | Timer not triggering spinning process | Replace the timer |
Reason 1 – Overloaded washer
Overloading the washer is a common mistake that people make, but it can cause the washing machine to not spin properly.
When the washer drum is overloaded, it puts too much strain on the motor and belt, which can prevent it from spinning clothes dry.
Overloading a washing machine can affect the spinning process in several ways. When clothes are packed too tightly in the washer drum, they can become unbalanced, causing the washing machine to shake and vibrate. This, in turn, can cause the load to shift during the spin cycle, resulting in the washing machine not being able to spin clothes dry. Additionally, an overloaded washer can damage the motor and belt, leading to costly repairs.
Tips on how to avoid overloading the washer
There are a few tips you can follow to avoid overloading the washer and ensure that it spins clothes dry.
Firstly, make sure to follow the manufacturer’s instructions when it comes to the maximum load capacity of the washing machine. Most top load washers have a maximum load capacity of around 18-20 pounds, so make sure not to exceed this amount.
Secondly, sort clothes by weight and fabric type before washing to ensure that the load is balanced. This will prevent clothes from becoming packed too tightly in the washer drum.
Lastly, consider doing smaller loads more frequently rather than one large load less often. This will not only prevent overloading but will also ensure that clothes are cleaned more effectively.
Maintaining proper balance during the spin cycle is important to ensure that clothes are spun dry and the washing machine doesn’t become damaged. An unbalanced load can cause the washing machine to shake and vibrate, resulting in the load shifting during the spin cycle.
This can cause the washing machine to stop spinning or not spin clothes dry. To avoid this, make sure to sort clothes by weight and fabric type before washing. Additionally, use the correct cycle for the load size and type of fabric to promote proper balance during the spin cycle.
Overall, overloading the washer is a common mistake that can cause the washing machine to not spin clothes dry. By following these tips and maintaining proper balance during the spin cycle, you can ensure that your washing machine works effectively and efficiently.
Reason 2 – Faulty lid switch
The lid switch on a GE top load washer plays a crucial role in ensuring that the spinning process functions as it should.
When the lid is closed, the switch signals to the machine to start spinning and when the lid is opened while the machine is still in operation, it puts an automatic stop to the spinning process. If the lid switch is faulty, your GE top load washer will not spin your clothes dry.
Signs of a faulty lid switch can range from simple to complicated. One of the primary symptoms is when the washer does not spin.
When you close the washer’s lid and press down on the switch, you should hear a click sound. If the machine doesn’t make this sound, it could indicate a malfunctioning lid switch.
Another symptom is when the washer starts to agitate even with the lid open. This is a clear sign that the lid switch needs replacement immediately.
If the lid switch has truly malfunctioned, the only solution is to replace it. To troubleshoot, unplug the washing machine and remove the screws that secure the control panel in place. Once the control panel is loose, lift it up slightly, and locate the lid switch within the machine. Check for any physical damage or disconnection. If the switch is disconnected, plug it back in. If there’s damage, it’s best to replace the entire switch.
To replace the lid switch, you’ll need to remove the top of your GE washing machine. This involves removing two screws on the bottom and two on the top that secure the top of the washer. Once you’ve removed these screws, push the washer top towards the back of the machine and lift it off.
You should be able to locate the lid switch and disconnect it. To install the new lid switch, simply follow the instructions provided by the manufacturer.
Points to remember:
- When the lid switch is faulty, your GE top load washer will not spin
- The lid switch signals to the machine to start spinning and stop spinning when the lid is opened
- Troubleshoot by checking for physical damage or disconnection. It’s best to replace the entire switch if damaged
- To install the new lid switch, follow the manufacturer’s instructions
Reason 3 – Unbalanced load
An unbalanced load in your GE top load washer can significantly affect spinning. When there is an unbalanced load, the washer drum may not be able to spin properly, causing it to shake or vibrate heavily.
This can lead to an uneven distribution of clothes within the drum, making it difficult or even impossible for the washer to spin them dry.
There are several tips on how to balance the load to ensure optimal spinning and avoid an unbalanced load.
First, make sure that you are not overloading the washer. If you are washing a large load, it would be better to split it into smaller loads to ensure that the washer drum has enough space for proper spinning.
Second, try to distribute the clothes evenly within the drum to avoid an unbalanced load. It is essential to place the heavier items, such as towels or blankets, at the bottom of the drum and distribute the lighter clothing items evenly on top of them. This ensures that the weight is distributed evenly throughout the drum.
Third, consider using a washer with an automatic load-balancing system. This system can automatically detect the weight and distribution of your laundry load and adjust the spin cycle accordingly to ensure proper spinning.
Lastly, make sure that the washer is levelled correctly. Place a level on top of the washer to ensure that it is not tilting to one side. If the washer is uneven, it can cause an unbalanced load that can affect the spinning performance.
Reason 4 – Broken drive belt
A drive belt is an essential component in the functioning of a GE top load washer. It connects the motor to the transmission and helps in spinning the clothes during the washing process. If the drive belt is broken, the washer will not be able to spin the clothes dry. In this section, we will look at the function of the drive belt, signs of a broken drive belt, and how to troubleshoot and replace it.
Function of Drive Belt in Spinning Process
The drive belt is responsible for transferring power from the motor to the transmission, which then transfers the power to the agitator and spin basket. When the washer is in the spin cycle, the motor rotates the drive belt, which in turn rotates the transmission shaft and motor pulleys. The belt also helps maintain the proper tension for the motor pulley and prevents it from slipping.
Signs of a Broken Drive Belt
The most obvious sign of a broken drive belt is when the washer does not spin clothes dry. You may also hear a loud noise coming from the washer during the spin cycle. If the belt is frayed or worn, it may slip off the pulleys or break apart. You can also visually inspect the belt for signs of damage or wear.
How to Troubleshoot and Replace the Drive Belt
Before replacing the drive belt, it is important to troubleshoot the problem to ensure that it is indeed the cause of the spinning issue. First, unplug the washer and remove the back panel to access the belt and other components. Check the belt for wear, cracks, or any signs of damage. If the belt is worn or damaged, it will need to be replaced.
To replace the drive belt, start by removing the old belt from the motor and transmission pulleys. Install the new belt in the same position as the old one, making sure it is properly seated on the pulleys. Rotate the motor pulley by hand to ensure that the belt is properly aligned and tensioned.
Reason 5 – Clogged drain pump
The drain pump in your GE top load washer is responsible for draining water out of the drum during the spin cycle. It plays a crucial role in the spinning process and if it becomes clogged, your washer may not be able to spin clothes dry. This can lead to your clothes coming out soaking wet and requiring extra drying time or even re-washing.
Signs of a clogged drain pump
The first sign that your drain pump may be clogged is water not draining properly from your washer. You may also notice a strange noise coming from the pump or a decrease in spinning speed during the cycle. If your washer is not draining at all, the drain pump could be completely blocked.
How to troubleshoot and clean the drain pump
If you suspect that the drain pump is clogged, the first step is to unplug the washer and turn off the water supply. Locate the pump and use a screwdriver to remove the screws holding the front panel in place. Carefully remove the panel and take a look at the pump.
You may see debris caught in the impeller or filter screen, preventing proper water flow. You can remove any visible debris by hand, but be sure to wear gloves and clear out any unwanted objects with caution. If the clog is not visible, you can use a wet/dry vacuum to clean out the pump.
Once you’ve cleaned the drain pump, reattach the front panel and test the washer. If water is still not draining correctly, you may need to replace the pump entirely. Contact a professional repair service for assistance with this process.
Reason 6 – Faulty motor coupling
The motor coupling is a small but crucial component of a washing machine’s spinning process. It connects the motor to the transmission, allowing the motor’s power to be transferred to the washer drum. If the motor coupling is faulty, the washer drum won’t be able to spin properly, resulting in clothes that are still wet after the wash cycle.
Signs of a Faulty Motor Coupling
One of the most common signs of a faulty motor coupling is a washing machine that fills with water but fails to agitate or spin. Other symptoms include an unusual noise coming from the washing machine during the spin cycle, leaking oil or grease, or a washer that stops working altogether.
Troubleshooting and Replacing the Motor Coupling
To troubleshoot a faulty motor coupling, first, unplug your washing machine from its power source. Locate the coupling by removing the washer’s cabinet or front panel, depending on the model you have. You’ll see the coupling between the motor and transmission. Check for any signs of damage, such as cracks or wear and tear. You can also try spinning the washer drum by hand. If it spins freely, the motor coupling is likely the culprit.
Replacing a motor coupling involves removing the existing coupling and installing a new one. You’ll need to purchase a replacement motor coupling that matches your washer’s make and model. You can find these parts at most home appliance stores or online.
To replace the motor coupling, first, unplug the washing machine and remove the cabinet or front panel. Then, remove the motor and transmission from the washer. You’ll need to detach the old motor coupling from both the motor and transmission, replacing it with the new coupling. Once the new coupling is in place, reassemble the washer and turn it on to test if it’s working properly.
Reason 7 – Worn out clutch assembly
The clutch assembly is an important component in the GE top load washer that plays a crucial role in the spinning process. It connects the transmission with the tub and helps the tub to spin. However, over time, the clutch assembly can wear out, causing the washer to stop spinning clothes dry. Here are some points to consider when dealing with a worn out clutch assembly.
Function of clutch assembly in spinning process
The clutch assembly is responsible for engaging and disengaging the transmission and the tub to allow the tub to spin during the high-speed spin cycle. The transmission is the part that powers the motor and operates the agitator. When the spin cycle begins, the clutch assembly engages the transmission and the tub to allow both to rotate together. As the tub rotates, the centrifugal force generated by the spinning water helps to remove the excess water from the clothes.
Signs of a worn out clutch assembly
The first sign of a worn out clutch assembly is a washer that fails to spin clothes dry. This is because the clutch assembly can no longer properly engage the transmission and the tub. Additionally, you may notice that the washer makes strange noises during the spin cycle or that the tub does not rotate smoothly. These signs indicate that the clutch assembly is either worn out or damaged.
How to troubleshoot and replace the clutch assembly
To troubleshoot the clutch assembly, first, unplug the washer and remove the motor and transmission assembly from the machine. Inspect the clutch assembly for signs of wear or damage. If necessary, replace the clutch assembly with a new one. To replace the clutch assembly, first remove the old clutch assembly and install the new one according to the manufacturer’s instructions. Then, reassemble the motor and transmission assembly and reinstall it back into the machine.
Reason 8 – Defective transmission
The transmission in a washing machine plays a crucial role in the spinning process. It sits between the motor and the drum, and its function involves controlling the rotation of the drum and agitator. If there is a problem with the transmission, it can cause the machine to stop spinning clothes dry. Here are some signs of a defective transmission and how to troubleshoot and replace it.
Signs of a defective transmission
- The machine makes a loud noise when operating or spinning.
- The machine doesn’t spin at all or struggles to turn the drum.
- The drum spins during wash and rinse cycles but not during the spin cycle.
- The machine vibrates excessively during the spin cycle.
- The agitator doesn’t move or rotates weakly.
How to troubleshoot and replace the transmission
- Unplug the machine and remove the front or back panel, depending on the model.
- Check for any visible damage to the belt, pulley, gears, or clutch.
- Use a multimeter to test the continuity of the washer parts such as the clutch, timer, water level switch, motor, etc.
- If the transmission is the problem, check whether it is repairable or requires replacement.
- Unbolt the transmission from the motor and the drum and remove it from the machine.
- Install a new transmission, making sure it’s compatible with the model and size of the washing machine.
- Reconnect the bolts, pulley, gears, clutch, and belt to the new transmission.
- Reinstall the front or back panel, plug in the machine, and test it to see if it is spinning clothes dry.
Reason 9 – Malfunctioning timer
One of the reasons why your GE top load washer may fail to spin your clothes dry is a malfunctioning timer. The timer controls the different processes that your washer undergoes, including the spinning process.
A malfunctioning timer can, therefore, fail to trigger the spinning process for your clothes to become dry.
You can identify a malfunctioning timer by observing some signs. For instance, if the timer fails to execute its functions, such as turning on the washer’s motor and the agitator, then it is a clear indication of a malfunctioning timer. Similarly, if the timer stalls halfway during a cycle or stops completely, then it may need to be replaced.
To troubleshoot a malfunctioning timer, you need to test its power supply using a multimeter. First, unplug your washer and remove the control panel. Locate the timer and disconnect the power supply wires connected to it. Use your multimeter to test the continuity of the timer. If there is no continuity, then your timer is faulty and needs to be replaced.
Replacing the timer requires you to remove the old timer and install the new one. First, disconnect the power supply to your washer and remove the control panel. Locate the faulty timer and remove it by unscrewing its mounting screws. Disconnect the wires connected to the timer and replace it with a new one. Reconnect the wires, and mount the new timer in place using the screws.
Conclusion
In conclusion, a GE top load washer not spinning clothes dry can be frustrating and time-consuming. However, there are several reasons why this problem can occur, and each requires a different solution.
From a malfunctioning lid switch to a damaged belt or transmission, it’s crucial to identify the root cause and address it immediately to avoid potential safety hazards or costly repairs.
By following the troubleshooting steps outlined in this article or seeking the help of a professional technician, you can ensure that your washer spins your clothes dry effectively and efficiently.
Don’t wait until the problem worsens or becomes irreversible – take action today and enjoy a hassle-free laundry experience.
Frequently Asked Questions (FAQs)
1. Why is my GE top load washer not spinning?
There may be several reasons why your GE top load washer is not spinning. It could be due to a faulty lid switch, a clogged drain pump, a malfunctioning transmission, or a broken drive belt.
2. Will a faulty lid switch prevent the washer from spinning?
Yes, a faulty lid switch can prevent the washer from spinning as it acts as a safety feature that prevents the washer from spinning with the lid open. If the lid switch is malfunctioning, it can interrupt the spin cycle, leaving your clothes wet.
3. How can I check the lid switch?
To check the lid switch, you need to open the washer’s lid and locate the switch near the lid hinge. Use a multimeter to test the switch for continuity. If the meter doesn’t show continuity when the switch is closed, then it needs to be replaced.
4. How can I unclog the drain pump?
The first step to unclog the drain pump is to unplug the washer. Next, locate the drain pump filter by removing the front panel. Once you find the filter, remove it and clean it. If the filter is excessively dirty, you may need to replace it.
5. What causes a broken drive belt?
The drive belt can break due to extended use or overloading the washer. Moreover, aggressive spinning due to an unbalanced load can cause the belt to slip off, causing it to break.
6. Can I replace the drive belt myself?
Yes, you can replace the drive belt yourself. However, it is essential to follow the manufacturer’s instructions and ensure you purchase a belt that matches the specifications for your washer.
7. What is transmission failure?
Transmission failure refers to the malfunctioning of the washer’s transmission, which is responsible for the washer’s spin cycle. Signs of a failing transmission can include strange noises, a washer that will not spin, and an oily residue on the floor.
8. Should I repair or replace the washer if the transmission fails?
If your washer’s transmission has failed, you might have to weigh repairing it against purchasing a new one. A transmission replacement can be costly, so if the washer is old and has a history of repairs, it might be more cost-effective to invest in a new one.
9. Is it essential to hire a professional to fix a washer that isn’t spinning?
While some washer repairs may require the expertise of a professional, issues like a clogged drain pump or a broken drive belt may be simple enough for you to fix yourself. However, if you are not comfortable with performing the repairs, it’s best to contact a professional to prevent further damage to the washer.
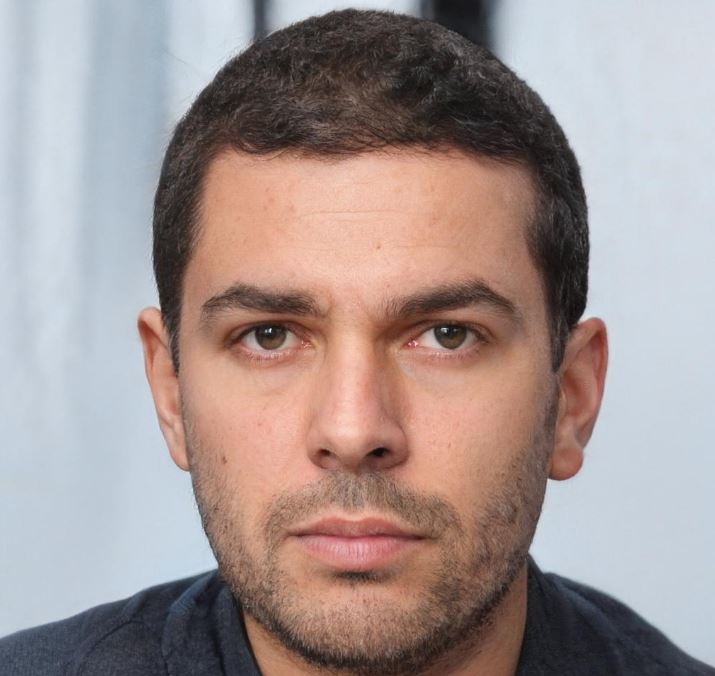
Joseph Short is a skilled home repair expert with a passion for do-it-yourself projects. With extensive experience in various home improvement areas, including carpentry, plumbing, and electrical work, Joseph enjoys sharing his knowledge and expertise to help others tackle their own DIY projects.
From fixing leaky faucets to renovating entire rooms, Joseph provides practical tips, step-by-step guides, and valuable insights to empower homeowners to successfully complete their home repair and improvement tasks.
With Joseph’s guidance, you can confidently take on your next DIY project and transform your house into a place you’re proud to call home.